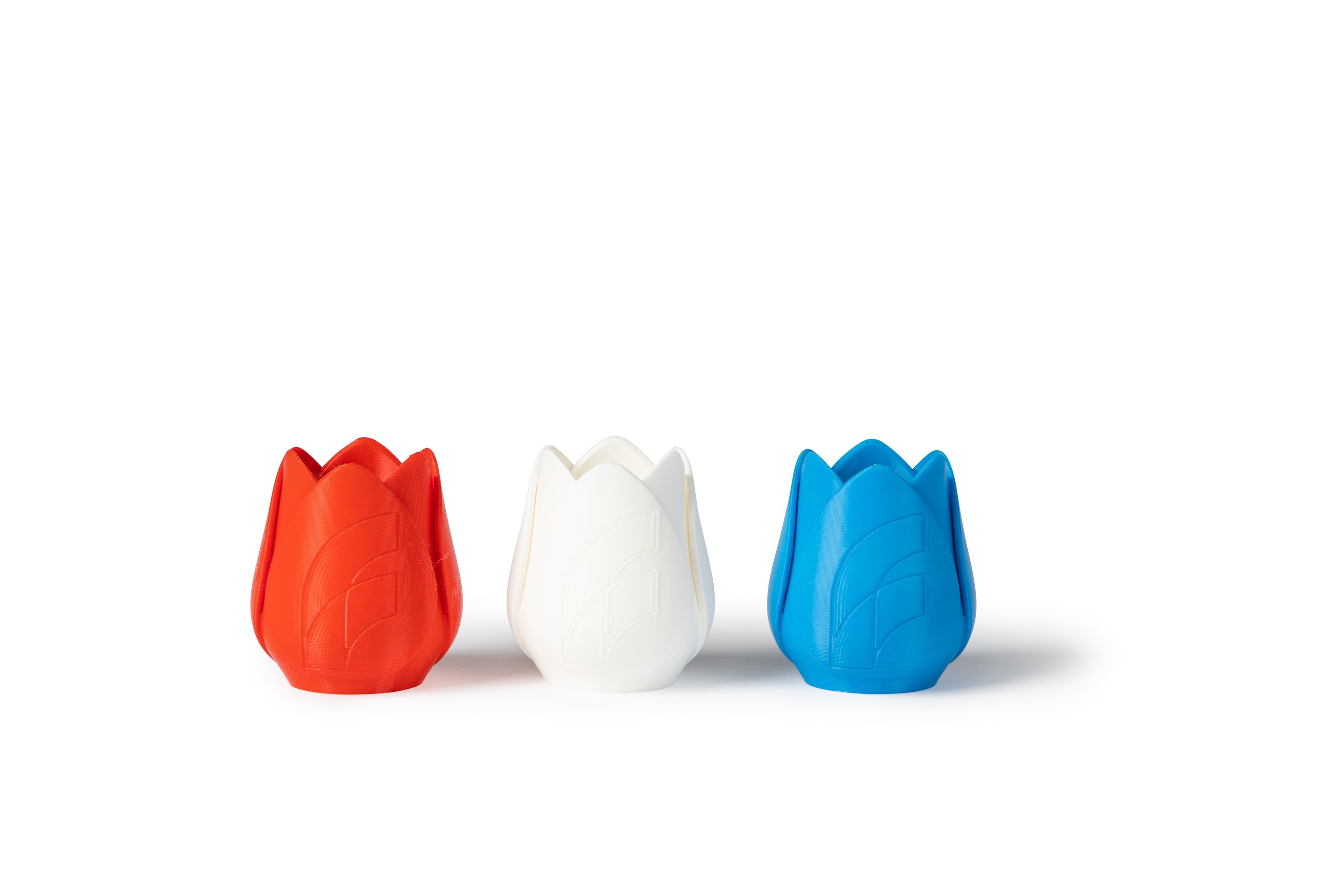
The Family of FELIXprinters AM Solutions Will Be On Show at TCT 2019
September 12, 2019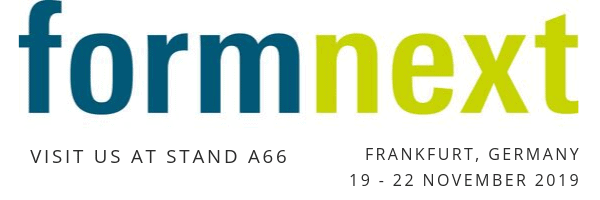
FELIXprinters to Make A Splash at Formnext
October 8, 2019Independent review states FELIXprinters’ Pro XL additive manufacturng platform is the first large volume printer tested that delivers the same quality and detail as Ultimaker.
FELIXprinters holds a strong position in the 3D printing /additive manufacturing sector, providing a range of industrially-oriented 3D printing platforms characterized by competitive accuracy, ease-of-use, and a range of build envelopes to accommodate numerous applications. However, with all the high-end features demanded when 3D printing is used as a manufacturing technology, FELIXprinters technology platforms are relatively low cost, and open up the possibility for companies to invest and bring 3D printing in-house rather than outsourcing.
In August, the largest build envelope machine in the FELIXprnters range — the Pro XL — was rigorously tested and independently assessed by Toon Meynen of full AM service provider company Trideus in Belgium. The results of the independent test reinforce the now widely held industry view that FELIXprinters is a serious and established high profile player when it comes to providing OEMs with industrial AM solutions.
Trideus recognized some of the key and unique aspects of the FELIX Pro XL, namely that it is constructed using aluminium extrusions making the bed very thin for a machine of its size (maximum build envelope: 600 x 400 x 600 mm), and the fact that the print surface is equipped with a removable flexible plate which makes removing any printed object “child’s play.”
Figure 1. The FELIX Pro XL flexible plate makes removing and printed part “childs play” according to independent analysis from Trideus.
Trideus also highlighted that the Pro XL comes with a large touchscreen, control via ethernet and WIFI, dual nozzle direct drive extruders with excellent part/filament cooling, solid moving mechanisms, fast bed-and print-head warming, USP power loss recovery, and it operates virtually silently (< 45dB) thanks to the modern electronics at its heart.
Here is a summary of Trideus’s findings:
- The user has the choice of using a web interface or the LCD screen on printer. Both are very clear and intuitive.
- Bed and nozzle calibration can be done via the interface and is easy to follow step-by-step.
- There is a Simplify license included with the purchase of the printer.
- FELIX support is excellent and every mail is answered quickly. Its location in the Netherlands is ideal for fast support both geographically and because of the ability to converse in multiple languages.
Trideus undertook a series of independent tests on the FELIX Pro XL machine.
The first was an “overall print quality test” benchmarking the FELIX Pro XL against the Ultimaker S5 machine. This test printed using PLA, a 200°C nozzle and a 45°C bed, 3DLAC adhesion, and a layer height of 0.2 mm.
Figures 2a,b, & c. Results of the Trideus “overall print quality” test, with FELIX parts on the left in each image and Ultimaker S5 parts on the right.
Trideus concluded that the cube, benchy, and polytower parts used in this test when printed on the FELIX Pro XL exhibited “high quality surface finish and details, overhangs and bridges were almost perfect, and when compared with the Ultimaker S5 parts, there was absolutely no difference between them.
Next, Trideus undertook a “multi-material print” test, using PLA and TPU95, again with a a 200°C nozzle and a 45°C bed and 3DLAC adhesion. Trideus recognized that this print was a “real challenge”, a 60 hour print using two differet materials. However, they concluded that “the print was extemely successful, and both materials had a neat surface finish.”
Figure 3.Results of the Trideus “multi-material print” test.
Next, Trideus undertook a “big object” testwith a 200°C nozzle and a 45°C bed, 3DLAC adhesion, and a chamber tempertaure of 0°C. Using the FELIX Pro XL, Trideus found that the rim was completed in 100 hours of printing, and the surface quality was described as “excellent”. In addition, Trideus reported that “the support material was easy to remove. To remove the print from the building plate is really great, you bend the steel sheet and everything comes off easily with that characteristic sound, really a pleasure to work with. It took 20 minutes to remove the support material from the FELIXprinters rim. In comparison, to remove the support material from the BigRep rim, took 2 hours.”
Figure 4. Results of the Trideus “big print” test.
Finally, Trideus undertook a “print with PETG material” test, using Polymaker Polylite PETG, a 235°C nozzle and a 80°C bed, 3DLAC and Brim adhesion, and a chamber tempertaure of 0°C. Trideus stated that the FELIX Pro XL printed the PETG “very well” and they stated that they were “very satisfied with the overhangs and details on the model.”
Figure 5. Results of the Trideus print with PETG material” test.
In general Trideus concluded that the FELIX Pro XL is a “high quality printer that is very versatile,” and benefits from its “automatic calibration, flexible build plate, large construction surface,” and the fact that it allows users to “print two materials with full confidence.”
Trideus did note that the accompanying documentation that comes with the FELIX Pro XL needed improvements, and that the power rescue mode was less than intuitive to use. The report, however, stated that “FELIXprinters is aware of these improvement areas and is working to deliver improved guides and videos to assist users with, for example, powerloss recovery. A series of instructional videos are busy being produced.”
The summary of the Trideus report is categoric in its praise for the FELIX Pro XL, and from an independent perspectve reinforces the general view that is building throughout industry today that FELIXprinters are a force to be reckoned with when looking to source sensitively costed but highly accurate and repeatable AM platforms. The report concludes, “This is the first large volume printer that delivers the same quality and detail as Ultimaker. This is the first time that we’ve tested a machine of this size that achieved that. Printing multiple materials is no problem for the this machine. The whole process of slicing, printing and finishing was very easy to do.“