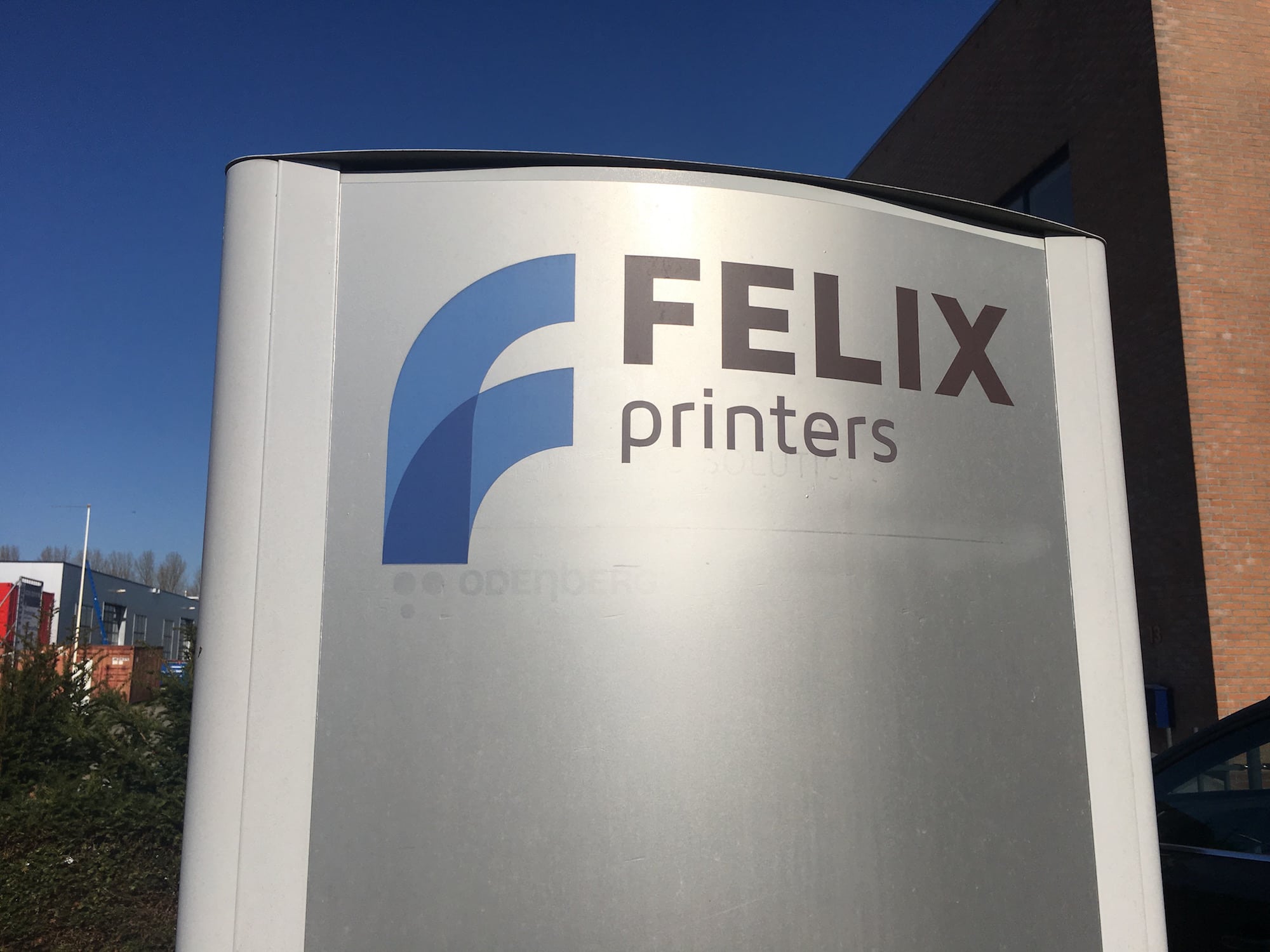
FELIXprinters Opens Up Company HQ to Press, Resellers and Customers
April 2, 2019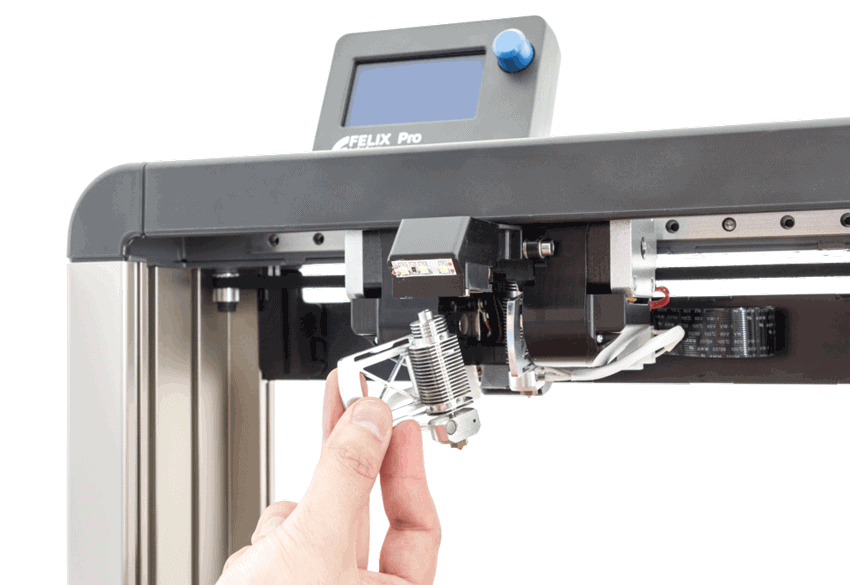
Recair Uses FELIXprinters’ Industrial Additive Manufacturing Platforms for Exacting Applications
May 17, 2019FELIXprinters is established as one of Europe’s leading manufacturers of highly accurate, reliable, easy-to-use, and price sensitive industrial 3D printing and Additive Manufacturing (AM) machines.
At an open day hosted at its HQ in the Netherlands about a month ago, the company’s profile in the industrial AM space as a provider of truly production-oriented AM platforms was cemented as it officially launched its next generation FELIX Pro L and Pro XL machines.
The Pro L and XL 3D printers have been developed withgreatly increased build volumes over previous FELIX AM platforms, the Pro L can build parts up to 300 x 400 x 400 mm, while the Pro XL has a build chamber of 600 x 400 x 600 mm To ensure the quality and reliability upon which FELIXprinters has built its reputation, both the Pro L and XL incorporate highly engineered print chambers, which include an enclosed warm zone and a cold zone. The warm zone supports consistent temperature control during the build, which is particularly important when printing materials with a high shrinkage factor, such as ABS, carbon fiber or Nylon. In contrast, the cool zone is where the electronics are housed, to prevent overheating and subsequent machine/build failure.
The Pro L and XL system also come with a range of automated and intelligent features that remove many of the tedious and time-consuming hurdles associated with additive manufacturing and speeding up the overall process. A stand-out example of this is the design of the dual nozzle. When the dual extruders are printing together they are at different print levels, avoiding any collisions and minimizing print failure. Moreover, if one nozzle is idle, it is automatically rotated out of the way so that there is no interference with the printed part, again avoiding damage to the print (and print failure).
There is another important aspect to the way that FELIXprinters serves industry with production AM solutions, and which makes it unique in the niche. Not only can customers purchase FELIX machines off-the-shelf, but the company can also build “tailor-made” AM platforms for specific customer applications.
Many AM platform vendors claim that they provide customized solutions, but in most instances, this implies the “tweaking” of off-the-shelf machines with various accessories. For FELIXprinters, tailor-made solutions means just that, an AM production solution built from the floor up to ensure it is optimized for customer applications.
The ability to do this builds on the exceptional R&D expertise exhibited by the FELIXprinters team, meaning that the company can work with customers to develop advanced bespoke 3D printing solutions. The company consistently encourages the formation of strategic partnerships with customers and other technology suppliers to ensure it is always at the vanguard of the advancement of innovation in 3D printing.
For obvious reasons, many of the tailor-made solutions that FELIXprinters has provided for customers are confidential. There are, however, two recent examples that show the nature of the relationship that FELIX establishes with customers to provide bespoke solutions.
In the area of 3D Bio Printers, FELIXprinters is at the moment an active participant in a fully funded EU project called “training4crm”. The goal of this project is to create an array of stemcells that can be applied to any cell, the initial goal being to find a cure for Parkinson’s disease by replacing brain cells. Ultimately, however, the technology can be used to cure or replace any cell type.
The consortium of institutions involved in “training4crm” consists of 10 individual parties, seven of which are universities and three commercial companies of which FELIXprinters is one. FELIXprinters has the task of supplying a 3D printing platform that can create the necessary cell arrays, create an extruder that is able to print biofluid, and create a hybrid printer that can print two materials at once. True customization.
FELIXprinters is involved in a number of R&D projects in the area of food printing. For the area, the open design of FELIXprinters’ AM platforms gives great freedom when it comes to experimenting with the printing of food. The use of a 3D printer in such applications leads to the production of novel shapes that cannot be achieved by conventional food processing technologies. It is also used for the production of small batches, and customized products.
FELIXprinters is also developing capabilities to provide fully modular printing stations, where print beds are automatically fed to the printer, and once the print job is complete the tray is transferred to an automatic FIFO buffer. A transport conveyor can be used to connect each module to the next, and in this way a fully integrated and automatic print-farm can been created.
The modules are linked via Ethernet, and controlled via a centralized control station, each module also having its own industrial control system and HMI touch panel. The system can accommodate multiple trays with a customized print area. If printing plastics the module uses 1.75 mm filaments of PLA, ABSX, PETG, wood and many more materials, and in the case of paste printing (for different material types), a customized FELIXprinters head can be used or one of a wide range of paste extruder heads.
Customers are invited to discuss any tailor-made solutions that they feel would benefit their projects with our team of expert 3D printing innovators.