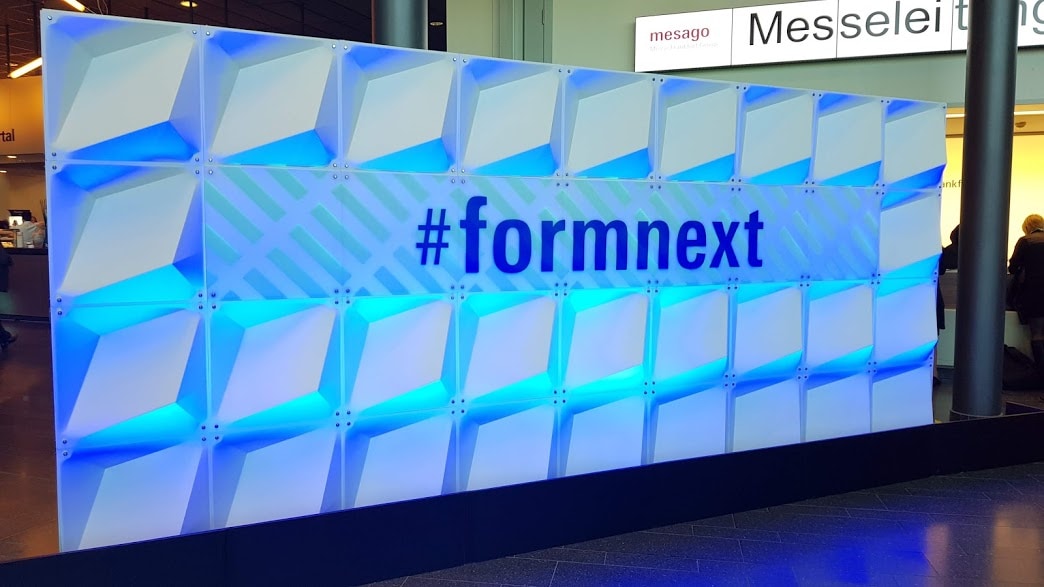
Major Success for FELIXprinters at Formnext
November 29, 2019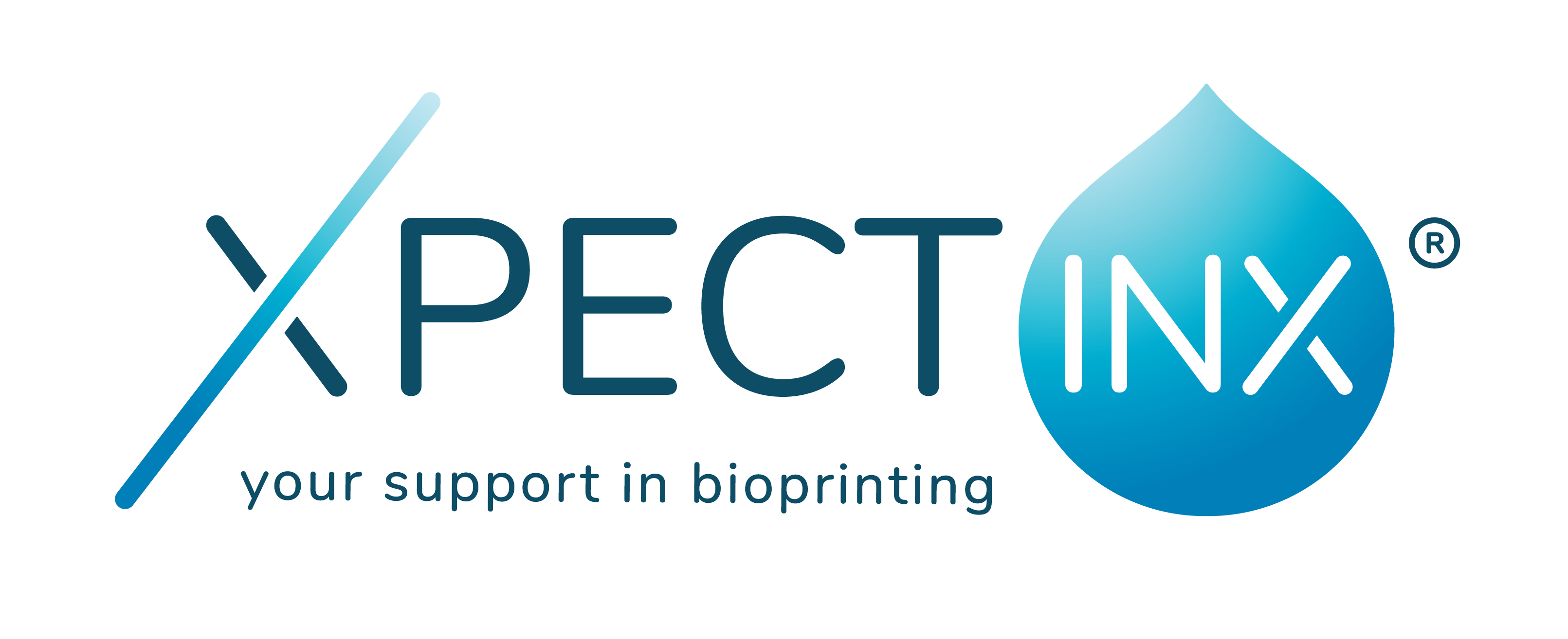
XPECT-INX Enters into Distribution Agreement with FELIXprinters
December 17, 2020After introducing its BIOprinter at the recent Formnext 2019 event in Frankfurt in November, FELIXprinters is delighted to announce that the machine is now commercially available, and pre-orders are already being processed.
The global 3D bioprinting market — currently valued at $965 million — is expected to grow at a CAGR of nearly 20% up to the mid 2020s, driven by increased healthcare demands, but also to overcome the supply bottlenecks and ethical issues associated with organ donation and tissue repair. Bioprinting also caters for the increased demand for customized patient-specific healthcare solutions, a trend that is only likely to accelerate moving forward.
FELIXprinters has established itself as a key player in the supply of mid-priced highly accurate industrial additive manufacturing (AM) machines, and has been independently assessed as the only credible rival to Ultimaker in terms of quality and cost-effectiveness in industrial AM*. The company’s reputation is built upon the Pro 3, Pro L, and Pro XL platforms, which are used throughout an array of industry sectors for challenging AM production applications.
The FELIX BIOprinter has been developed on the chassis of the established FELIXprinters product line, meaning that at its heart is the tried and tested technology that has already been serving manufacturers for years. The printer is characterized by key features that are specifically designed for medical, scientific, and research applications, including syringe cooling, print bed cooling and heating, a dual head system, easy syringe positioning (ergonomic access to the machine supports researchers in their work), and automatic bed levelling.
Wilgo Feliksdal, Co-Founder of FELIXprinters says, “The BIOprinter has been designed to be the ultimate bio research instrument in a cost-effective package. It has been developed alongside the brightest minds in the bioprinting sector, and we partnered with training4crm and the Technical University of Denmark (DTU), and received funding from the European Union Horizon 2020 Programme to develop the BIOprinter. Uniquely, the BIOprinter combines dual sterilizable printheads which have a modular design for easy changeovers, and separate heads are available to print different bio-inks at the same time. This integrates different material properties into a single scaffold structure.”
The BIOprinter has automatic bed levelling through the use of a unique probing systems which results in a perfect first layer, which means a quality end result. The BIOprinter also retracts with a highly precise motor for better dosage or materials and more accurate material flow versus alternative air pressure systems.
Feliksdal continues, “The BIOprinter consists of an adaptable and flexible ecosystem to ensure that it can meet a wide range of researchers’ needs without generating unnecessary costs. One major advantage is the source control system which enables the user to use standard slicing software and make changes themselves if needed. Also, syringes are not restricted to expensive brand-specific or in-house produced products that essentially drive up operating costs. The machine instead has been designed to use a standard 5ml syringe, and standardized petri dishes and culture plates, so there are no limitations on auxiliary parts and materials.
Users of the BIOprinter benefit from the fact that print heads are easy to sterilize, which eliminates the likelihood of contamination. The BIOprinter is hand-made in the Netherlands, and has undergone testing for 24 hours before being issued with CE certification. The machine is WIFI and LAN enabled, comes with a one-year warranty, and lifetime customer support.
The FELIX BIO is appropriate for all types of bio-printing research, and is equipped with strong motors that can extrude a range of different viscosity of materials. In addition, the BIOprinter has been designed to be easily upgradeable, which means that the lifecycle of the machine can be extended without compromising quality, reliability, and productivity.
* Toon Meynen, Trideus, Belgium, 2019.